WAW-600G microcomputer controlled electro-hydraulic servo universal test machine
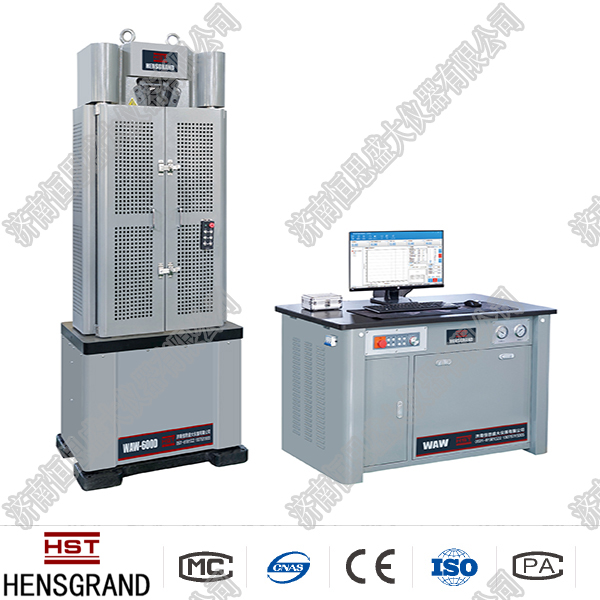
WAW-600G microcomputer controlled electro-hydraulic servo universal test machine

This machine has a four-column, double lead screw, and a cylinder under-mounted main machine structure, the jaw seat is a semi-open structure, and the control oil source is a piano-type oil source control cabinet. The tensile space is located above the host, and the compression, bending and shear tests are located below the host, that is, between the moving beam and the workbench. The adjustment of the test space is achieved by moving the position of the middle beam. The movement of the middle beam uses a gear reducer motor to drive the chain transmission. The computer automatically controls the servo valve to complete the loading process of the sample, and has a variety of automatic control methods such as constant rate test force, constant rate deformation, and constant rate displacement. Smooth switching can be achieved between various control methods. The independent external controller and strong electric control system provide strong guarantees for the stable operation of the equipment. After the test is completed, the computer can automatically calculate the test results of the material's elastic modulus, tensile strength, upper and lower yield strength, specified non-proportional extension strength, maximum force total elongation, after-break elongation and cross-section shrinkage, and can directly output standard test reports and test curves, or output statistical reports in EXCELL and WORD formats.
Performance Features
1. The host adopts a four-column high-rigid frame structure, which has stable support, stable loading and beautiful appearance;
2. The host base is precision cast using QT500-7 to reduce equipment operation noise and improve equipment rigidity;
3. Both the moving beam and the upper beam are precision cast and CNC precision machining to ensure the neutrality of the sample clamping;
4. The mobile beam lifting system uses grinding lead screws and precision gear reducers to reduce the noise generated when the beam lifts and lowers;
5. The semi-open jaw seat prevents damage due to the trumpet-shaped deformation of the jaw seat, which improves the service life of the equipment;
6. The jaw adopts a dovetail groove structure, with a hardness of up to 58-62HRC, which has the advantages of convenient installation and durability;
7. The measurement and control system has a fast running speed, a gentle interface, and has multiple sample information input modes, which can meet the test of different materials; 8. The sample information is convenient to enter, and the test of multiple samples can be completed at one time after inputting sample information of the same conditions;
9. Samples with the same conditions can be superimposed on various test curves, which can clearly identify the stability of the material;
10. The accuracy of the test force and deformation display is as high as 1/500,000, and the full range display resolution remains unchanged to ensure the accuracy of measurement;
11. Test force, displacement, deformation, loading rate and various test curves are displayed dynamically in real time on the screen as the test process;
12. The loading method of the test process can be controlled by free editing programs according to the customer's idea;
13. The experimental results can realize resource sharing among local networks;
14. Automatic overload protection shutdown when the load exceeds 3-5% of the full scale.
Main indicators
Product model | WAW-600G |
Host structure form | Dovetail groove jaw + four columns + double screw + full protection + main cylinder underlay |
Maximum test force | 600kN |
Test machine level | Level 1 or Level 0.5 |
Test force measurement range | 2%-100%FS |
Relative error of test force display value | ±1% or ±0.5% of the displayed value |
Displacement display accuracy | 0.01mm |
Displacement measurement accuracy | ±0.5% |
Deformation display accuracy | 0.001mm |
Deformation measurement accuracy | ±0.5% |
Control method | Servo valve automatically controls constant force, constant displacement and constant deformation and loading methods |
Crossbeam movement speed | About 220mm/min |
Maximum piston speed | 90mm/min |
Piston stroke | 250mm |
Stretch space/compression space | 1350/1000mm |
Left and left spacing of columns | 580 |
Sample clamping method | Hydraulic automatic clamping |
Steel strand specimen diameter | 1*7 type Φ9.5-21.6mm |
Rebar specimen diameter | Φ13-45mm |
Up and down pressure plate | The diameter of the circular pressure plate is 160mm, and the down pressure plate is adjusted with spherical surface |
Control the size of the oil source | 1200*675*780mm |
Host size (mm) | 860×740×2575 |
Power supply | Three-phase five-wire system, 380V/50Hz |
Power supply | 3.0kW |
Recommended informationNEWS
- [2022-09-28]What issues should be paid attention to when maintaining a hydraulic universal testing machine?
- [2022-09-28]What should be noted when using the repetitive bending test machine for steel bars?
- [2022-09-28]Main uses and daily maintenance of spring tester
- [2022-09-28]How should the pressure tester be operated and calibrated
- [2022-09-22]How should the pressure tester be operated and calibrated
- [2022-09-09]Performance characteristics of insulator horizontal tensile testing machine
- [2022-09-09]Basic functions of terminal tension testing machine
- [2022-09-09]Operation method and characteristics of cup protrusion test machine
- [2022-09-09]Tear test of various samples by electronic universal testing machine
- [2022-09-09]How to choose the internal structure of the tensile tester
- [2022-09-02]Daily maintenance of test machines
- [2022-09-02]Research and development trends of spring test machines
- [2022-09-02]Working principle of anchor chain tension testing machine
- [2022-08-26]Advantages of universal tensile testing machine
- [2022-08-26]Do you know how important the configuration of the universal tensile test machine is? The configuration of the universal tensile test machine
- [2022-08-26]Introduction to the functions of the repeated bending test machine of metal material
- [2022-08-26]How to use the universal tensile testing machine?
- [2022-08-26]What are the key points of the lateral deformation test of electronic universal testing machines?